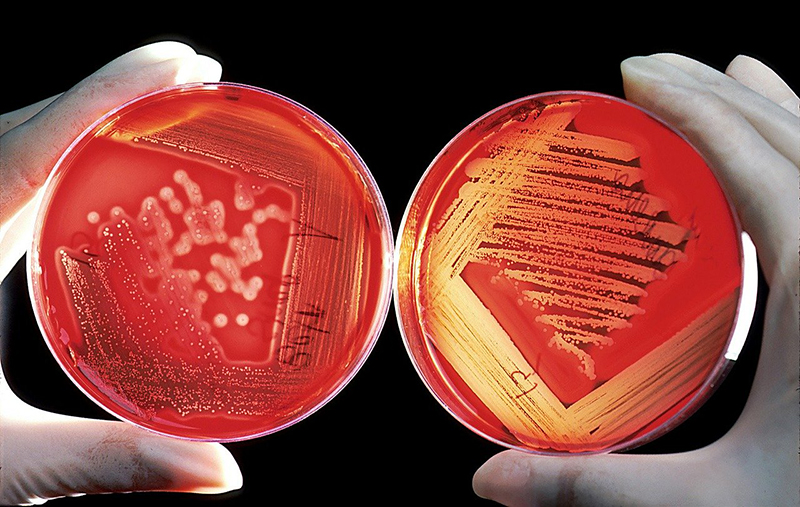
To yield sufficient oral drug bioavailability, poorly soluble drugs often require “enabling formulation technology”. Spray dried dispersions (SDDs) are one such enabling technology. SDDs exhibit poor flowability, small particle size, and low bulk density. Hence, capsules are often not viable, such that dry granulation is typically required to fabricate tablets from SDDs. Manufacturing tablets of SDDs requires powder compaction, at each the slugging (or roller compaction) stage and the tableting stage. Hence, compaction is a major unit operation for formulations of poorly soluble drugs that employ SDDs. However, emerging observations across the industry point towards high sensitivity of tablets from SDDs to compaction factors. There is a need to understand the solid state compaction properties of spray dried dispersions.
Project Description and Goals
Tablet compacts will be manufactured using a compaction simulator, where compacts will be made of SDDs or simple mixture of drug an polymer (i.e. not spray dried dispersions). Drug will be itraconazole. Polymer will be various grades of hydroxypropyl methylcellulose acetate succinate (HPMCAS). A full factorial design will be carried out to assess impact of polymer type, compaction speed, and compaction thickness on solid state properties of spray dried dispersions. Compacts will be characterized with respect to their solid state compaction properties, to elucidate the effect of spray drying. Results are expected to yield insight into compact integrity, including its sensitivity to compaction variables, which will contribute to product quality of these complex formulations.
Top